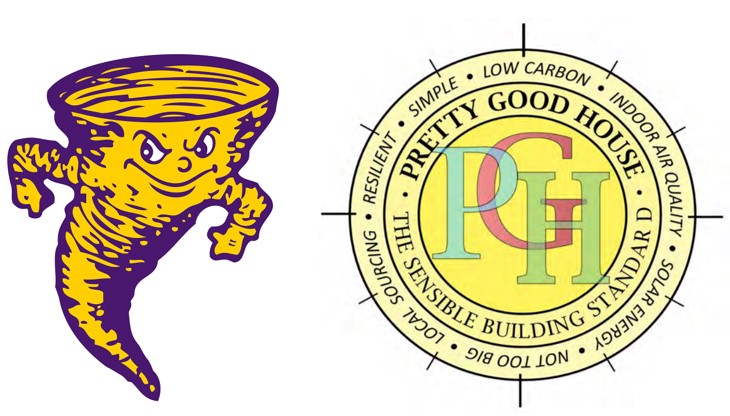
(Follow THS PGH project activities on Matt’s Build_Learn_Teach Instagram)
The school year is underway, and Matt Blomquist’s Taylorville High School students in central Illinois are busy building a strong foundation for their new PGH (Pretty Good House) project.
THS students are also building a strong foundation for their futures under Matt’s guidance. Skills are being developed ranging from physical building skills to “meta-skills”, the mental ability to think through a complex construction project: organizational skills, team building, and ability to work through difficult problems. Matt’s students, their children, and beyond will be able to drive by this house with a feeling of accomplishment.
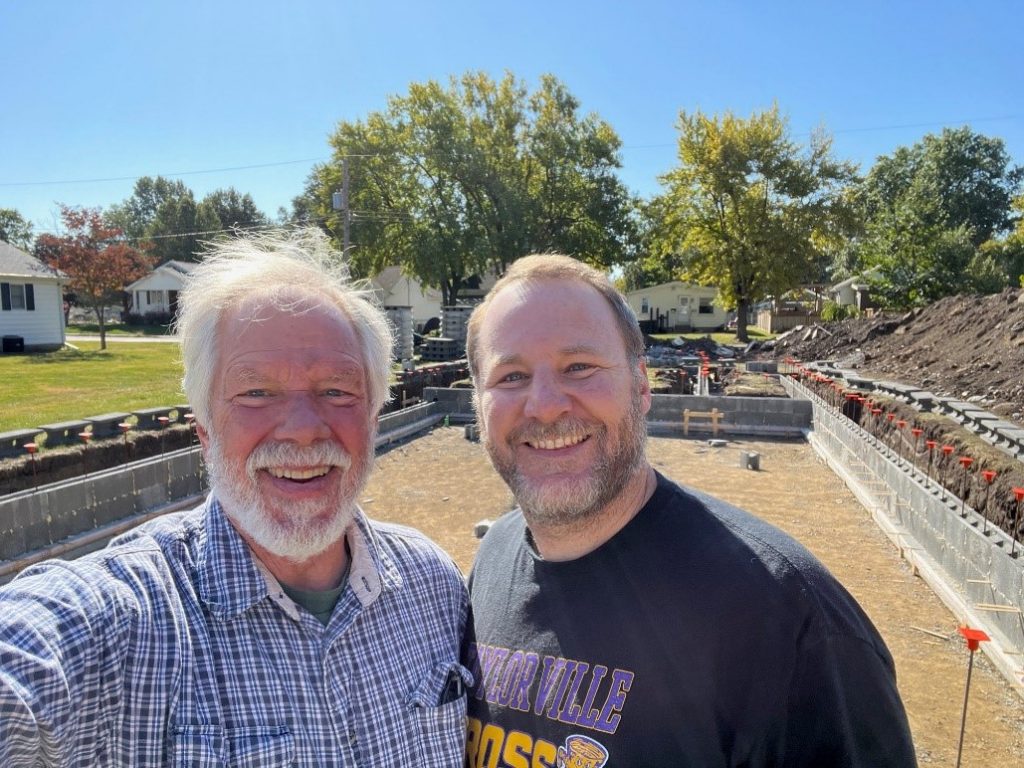
Our initial article introduced the project and presented the economic justification of PGH design. As we follow Matt’s progress each month, we’ll cover a variety of topics including the home’s energy performance, “Manual J” mechanical equipment sizing (heating, cooling and dehumidification), duct design, and installation of the “mechanicals”. Build Equinox is donating a CERV2 to the THS PGH project, and providing HVAC engineering design and installation expertise. Build Equinox appreciates working with Matt. We are learning a lot, too! We plan to create an instructional series with Matt to help others learn how to design healthy, comfortable, economical, affordable, energy efficient, net zero homes! That’s a lot of adjectives, but each one is its own discussion topic.
Taylorville High School Tech Ed House Construction Program
I pestered Matt with a number of questions about the THS house construction program to understand its organization and cost. Every community should be educating future skilled workers for their community’s construction trade needs. Matt told me his students are in demand and readily find employment. Beyond the construction industry, his students also find jobs with utilities, facility maintenance, and manufacturing.
The THS construction curriculum consists of a morning class group and an afternoon class group with primarily juniors and seniors. High school student participants earn credit that can count for community college coursework. Matt has also created an opportunity for the local community college to have a Monday evening class participate in construction activities. This fall’s enrollment consists of 11 students in the morning session, 14 students in the afternoon class session, and 9 students for the Monday evening community college session.
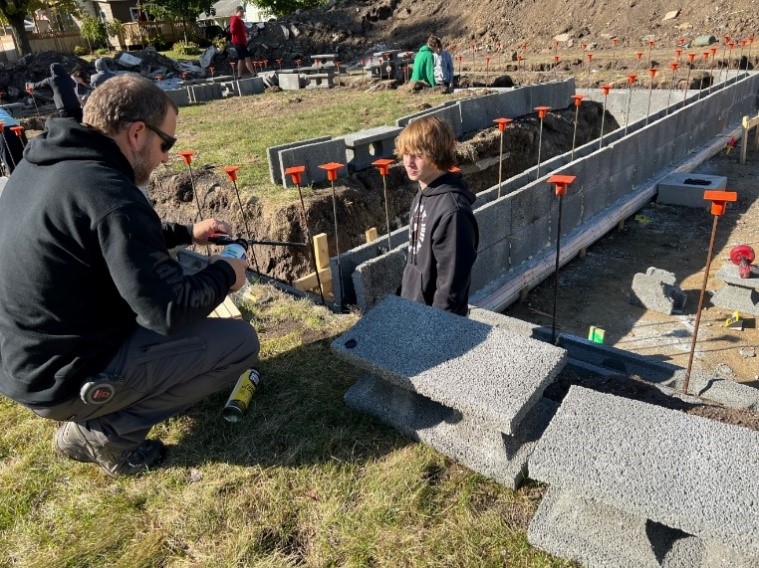
Although this seems 33 students sounds like a very large construction workforce for one home, a lot of time is spent teaching how to do everything…from using an array of tools, safety, planning the day’s work activities, organizing work groups, and training students about properly dressing for a work site. Yes, Matt instructs students on jobsite clothing; wearing layers to stay comfortable as the weather and physical activities vary throughout the day. We no longer have farm kids and backyard mechanics feeding into our technical education programs that already have basic tool skills, so many students start from very basic levels.
I asked Matt about the budget and he told me it is roughly $200,000 per house project, which does not include his salary. He raises in kind donations (such as a CERV2, and other mechanicals that our Build Equinox manufacturing friends are providing to the project). Matt uses projects to try new technologies such as “Perfect Block” and “Fast Foot” that are described in the next section.
Taylorville High School’s previous house (see MLS listing CA1025199) is now on the market, and Matt expects it to readily sell. The 1672sqft, 3 bedroom, 2 bath home is listed at $219,900.
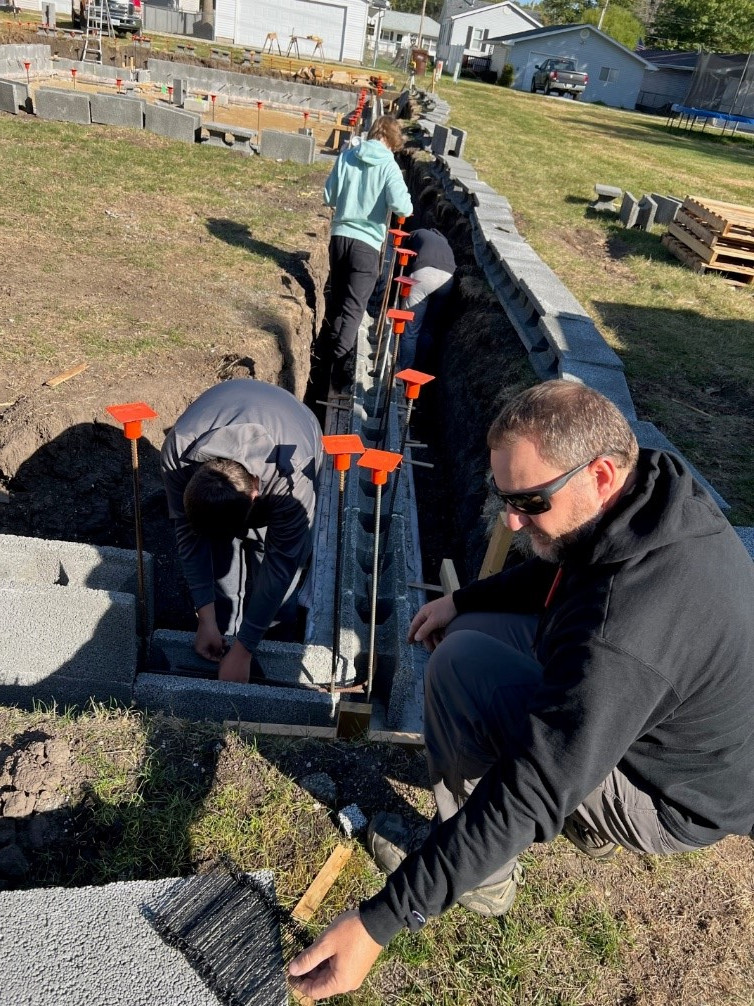
Matt gave me a tour of the home, and I was really impressed with the fit and finish, and overall quality. These novice students have built a wonderful home that they, their children and grandchildren can drive by with a well-deserved feeling of pride and sense of accomplishment.
Something new this year is the Inflation Reduction Act (IRA) allowing tax exempt groups, such as schools and religious organizations, to receive “tax credits” for installation of solar PV and other energy efficiency measures. Including Illinois’ Solar Renewable Energy Credits (SRECs….”S-wrecks”), THS PGH expense for solar PV should be reduced by 50%. With THS PGH students supplying “free labor”, the net installed cost is only 75 cents per watt!
Current THS PGH Activities
(note: Matt’s Build_Learn_Teach Instagram site is a great way to follow activities)
I visited Matt and his morning class at the worksite on October 10 to watch Matt’s class in action. Students were working in two to three groups around the foundation, stacking and applying urethane adhesive to the Perfect Block foundation (see Figures 2 and 3). Perfect Block is described as an “ICCF”, an insulated composite concrete form. The blocks are concrete composite blocks made from recycled Styrofoam with a concrete binder. The manufacturer states that their Styrofoam is 100% recycled and is 90% of the block material volume (the Arizona company welcomes Styrofoam donations, too).
Urethane foam guns inject a small amount of foam adhesive between block seams, forming a structure for pouring concrete.
Unlike ICF (insulated concrete forms), the ICCF has horizontal and vertical tunnels. Rebar is laid horizontally and placed vertically in the blocks such that a concrete “post-n-beam” structure is formed rather than a concrete wall as in ICF construction. Unlike ICF blocks that have “lego-like” block connections, ICCF blocks are stacked on top of one-another without inter-block locking. The blocks are easily rasped or shimmed for keeping block courses level. Matt had students leveling each course as they progressed.
Matt said their cost for the Perfect Block foundation was $10,000, including $3000 for shipping from Arizona.
(Note: products mentioned by Build Equinox are not endorsements, and we receive no compensation…we are simply providing information for interested readers).
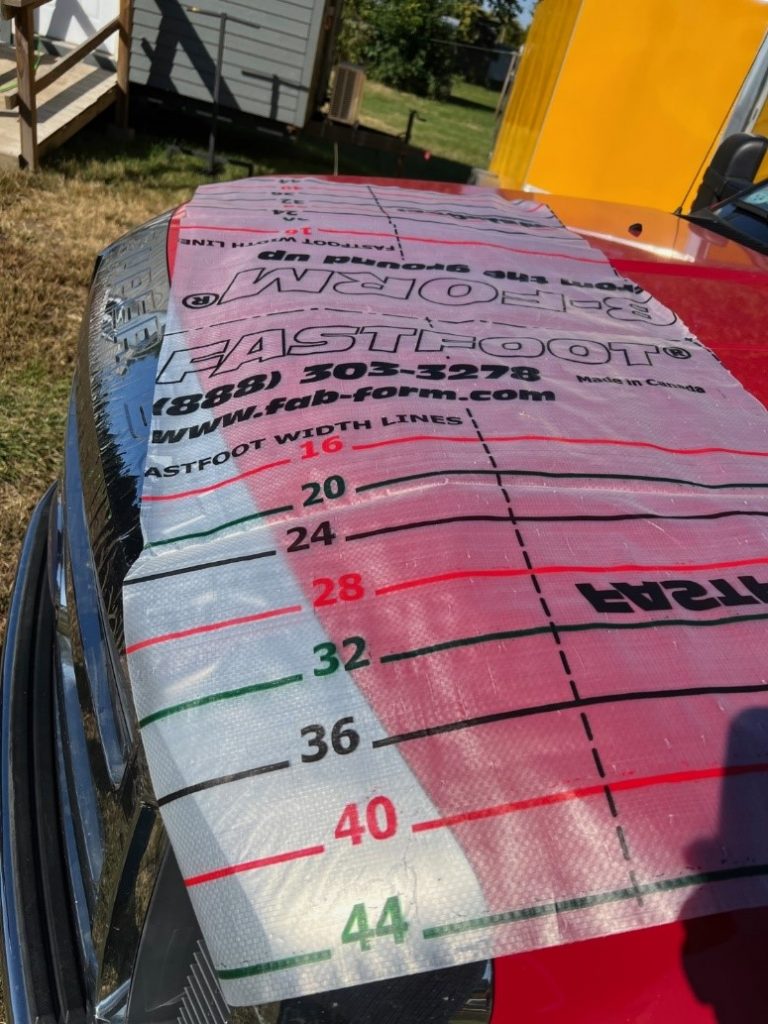
Another product Matt is using for the first time is “Fast Foot” fabric for footers. Matt said the footer form system was easy to use, speeds up the footer forming process, and produces a quality footer. 2x4 horizontal rails are leveled around the house perimeter in the footer trench. The Fast Foot fabric has a tough skrim embedded in it, so that it is tough and flexible.
Lines are marked on the fabric, with a “zero” line marked down the middle that should roughly aligned with the middle of the footer trench. A line number is chosen for a given footer dimension (eg, 36”), and that line is placed along the top edge of the 2x4 boards. The fabric is fastened to the top of the 2x4s with the leveling line chosen such that the fabric has sufficient slack to form a rectangular base on the ground. Concrete is poured to filled the Fast Foot “bag”, which bulges slightly on its sides.
Keep following Matt’s team and our continued articles to see a healthy, energy efficient, economical net zero dream house become reality!